
Pioneering Perfection:
Cutting-Edge Float and Pattern Glass Manufacturing.
The New Standard in Glass Manufacturing
Efficient Eco-Friendly Innovation Unleashed.
At Wallace MacDonald, our Research and Development department, in collaboration with HORN®, is dedicated to enhancing the efficiency and customer-friendliness of plant components and materials. Our focus extends beyond customer orientation to encompass ecological considerations as well.
One prime example of this commitment is the optimization of the GCS® 301-advanced series feeders in sizes K36-K54. By improving the insulation of the channel blocks and adopting a more compact, modular design, we have significantly reduced wall losses. This optimization leads to higher thermal homogeneity and a lower specific energy input.
Moreover, we have standardized the superstructure of these feeders, resulting in cost savings in production. This holistic approach ensures that our innovations are not only technologically advanced but also environmentally responsible and cost-effective.
Astrophysics & Energy
Excellence in PECVD
Aug 29, 2025
Sep 5, 2025
10 - 11:30 am
Advanced Integrated Process
Manufacturing Innovated
Aug 28, 2025
Sep 4, 2025
10 - 11:30 am
Vertically Integrated Solar
PV Value Chain
Aug 27, 2025
Sep 3, 2025
10 - 11:30 am
HJT-TOPcon-Perovskite
Genesis Fusion Solar Cell Technology
Aug 26, 2025
Sep 2, 2025
10 - 11:30 am
Genesis Fusion Manufacturing
QX Epitaxial Wafers for Semiconductors
Aug 25, 2025
Sep 1, 2025
10 - 11:30 am
Wallace Glass Melting Technology
Wallace MacDonald's cutting-edge 3.5 million sq ft technology complex, the largest in the USA, is coming to Nevada. In partnership with Horn Glass Industries, we are bringing the largest Float and Pattern Glass manufacturing facility in the country.
Our state-of-the-art complex is designed to elevate your business by integrating the latest technological advancements. Specializing in the design, development, and manufacturing of next-generation aerospace systems and propulsion devices, our complex will feature advanced laboratories and manufacturing units equipped with the latest innovations in aerospace engineering, energy-efficient propulsion systems, and integrated aerospace solutions.
Float glass furnaces are the largest type, both with regard to dimensions and overall melting output. These furnaces are close to the limit of constructive possibilities, with capacities typically ranging between 600 – 800 tons per day (t/d). Smaller units with 250 t/d and larger units up to 1200 t/d are also possible. Float glass furnaces are especially designed for the production of soda lime glass, with stricter quality requirements compared to container glass.
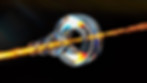

Float glass furnaces are usually cross-fired furnaces. The regenerators, port necks, and burners are arranged laterally. For each port neck, there is a separate regenerator chamber together with a slide at the flue gas channel.
This allows precise control of the furnace temperature over the entire length of the melting furnace. The firing is usually facilitated with underport burners. Oxyfuel burners installed in the sidewall near the charging zone are called zero-port boosting.
This is a measure to increase melting capacity without enlarging the regenerator structure. Float glass furnaces are constructed as open furnaces. A clear separation of the hot melting part and refining part and of the working end is not possible, as this would lead to optical defects in the glass.
Our engineers will leverage breakthrough materials, such as high-performance composites and advanced alloys, to develop the propulsion devices of the future, including electric propulsion systems, hybrid engines, and other cutting-edge aerospace technologies. These advancements will not only meet but exceed the demands of future aerospace missions.
The facility will also integrate automated and intelligent manufacturing processes, including precision machining, additive manufacturing (3D printing), and advanced assembly lines. This will ensure the highest levels of quality, efficiency, and scalability in production, positioning us as leaders in the aerospace industry and driving forward technological progress in both commercial and defense aerospace sectors.
By partnering with Wallace MacDonald and Horn Glass Industries, you'll have access to unparalleled resources and expertise, empowering your business to stay at the forefront of technology and innovation.

About Us
Our state-of-the-art glass manufacturing facility at Wallace MacDonald leverages a data-driven approach to solve the challenges faced by modern businesses. We partner with companies of all sizes, across various industries, to help them achieve their goals and aspirations through cutting-edge glass solutions.
Our team is passionate about providing customized manufacturing solutions, tailored to the unique needs of each of our clients. Whether it's float glass, pattern glass, or innovative glass technologies, Wallace MacDonald's advanced facilities and expert engineers are here to elevate your business.
